Molinos coloidales
Resuelva su problema de emulsión reduciendo sus costos y aumentando su productividad
Acerca de
- Historia
- Elección del mezclador
- Tipo de equipamiento
Los primeros molinos coloidales fueron fabricados en Alemania en los años 30. Originalmente fueron
rotor de varias etapas y siempre su diseño era cónico. En los 70 mejora el diseño para rotores / estatores de una
sola etapa. Los materiales utilizados para la fabricación son acero inoxidable AISI 316, pudiendo usar diferentes
aleaciones de acero que aumentan la duración del rotor / estator.
Los molinos coloidales se utilizan generalmente para hacer emulsiones. La manufactura también puede enriquecer
progresivamente la fase de dispersión.
El principio básico consiste en la acción que produce un rotor estriado al girar a 3.000 rpm contra un estator fijo
también estriado, siendo sometido el producto a procesar a fuertes acciones de corte y rozamiento. Los platos de
especial diseño son construidos en acero, cromo níquel, acero inoxidable 304 / 316 o 420 templables. La
regulación de los platos se efectúa mediante un volante ó un sistema de regulación que permite graduar la
separación y aproximación entre los platos. El diseño de paletas centrifugadoras hace el efecto de bomba
impulsando el producto a través de cañerías pudiendo elevarlo hasta una altura determinada funcionando el
molino como bomba.
Hay que tener en cuenta el resultado específico que ha de conseguirse con la mezcla.
Así, un agitador que sea satisfactorio para estimular la disolución de sólidos solubles en un líquido puede no ser
eficaz para mantener sólidos insolubles en una suspensión uniforme.
En muchos casos, el agitador puede necesitarse para realizar dos o más funciones simultáneas:
Buen contacto entre líquidos inmiscibles y al mismo tiempo, ha de estimular la transmisión efectiva de calor al
interior del material y desde él.
La selección del mezclador apropiado dependerá también del medio en que se haya de trabajar; ya sea un gas, un
líquido o una masa de partículas sólidas; bien sea homogéneo o heterogéneo con respecto a las fases; o las
fases; o bien de alta o baja consistencia.
El diseño o proyecto de un agitador exige la especificación del tipo de aparato, las dimensiones y proporciones del
elemento mezclador, la situación de este elemento dentro de este recipiente para la mezcla y las condiciones de
funcionamiento del agitador. En general, el mezclador óptimo, al igual que el equipo óptimo para otras
operaciones unitarias, será el que consiga el resultado deseado con la combinación más económica de cargas
fijas y de funcionamiento.
En la práctica se selecciona corrientemente el dispersor que asegura resultados más efectivos y sea más atractivo
desde los puntos de vista de su costo instalado y de su conservación, ya que la energía consumida en la mezcla
es frecuentemente sólo una pequeña parte de la necesaria para todo el proceso.
No obstante, el proyectista minucioso investigará las necesidades de energía, particularmente en las operaciones
que exijan dispersores de gran potencia. El tipo, o los tipos, las dimensiones y la posición del agitador para la
operación se determinan primero partiendo de los principios empíricos generales. Luego se especifican las
condiciones de funcionamiento; éstas son menos fáciles de generalizar y se deducen por la experiencia del
ingeniero o del vendedor del equipo, o bien por medio de ensayos de modelos.
Aunque existen una gran variedad de mezcladores y dispersores en el mercado, estos
pueden ser divididos en aplicaciones de bajo y alto esfuerzo de corte. En la forma, típicamente paletas o tipo
propulsores, la reducción del tamaño de la partícula no toma lugar, la acción es realizada por el derretimiento y/o
disolución.
El mezclador sirve para mantener la homogeneidad de la composición y la uniformidad de la temperatura,
proveyendo un pequeño aumento en sí mismo. En el último caso, existe un paso en el cual las partículas son
físicamente reducidas en tamaño por el corte mecánico/hidrodinámico con la combinación del rotor/estator
acompañado por un pequeño aumento de la temperatura por la energía de mezclado.
Tales equipamientos, aun funcionando con tamaño de partículas superiores a pelletas, proveen rápida y eficiente
dispersión y mezclado.
Equipamiento de alto esfuerzo de corte existen de dos maneras diferentes, tipo inmersión vertical y el del
mezclado en línea.
* El vertical, el rotor/estator está montado sobre una plataforma e inmerso en un tanque de material, dependiendo
del cabezal mezclador para circular la mezcla y asegurar homogeneidad.
* El caso del mezclado en línea, la combinación del mezclado en un tanque recirculando por una bomba molino.
Experiencias han demostrado que este tipo de equipamiento, lo cual asegura una total disolución, da una mayor
rapidez y performance que la desintegración con un solo mezclador vertical, especialmente para grandes
volúmenes de producción, tanques mayores a 25 toneladas.
Buscando una solución adecuada para tu empresa?
Características técnicas
- Rotores disponibles: Dientes normales, cruzados
- Montaje: En base móvil o fija, para operación en vertical, horizontal o ambos.
- Conexión del eje: Juntas de acrílico-nitrilo, Viton o sellado mecánico.
- Construcción: De acuerdo con normas estrictamente sanitarias.
- Motor eléctrico: Motores asíncronos trifásicos IP 65, a pedido anti explosivo.
- Protección: Carcasa del motor de protección de acero inoxidable.
- Material: Acero inoxidable AISI 304, 316, 420 o 430 con certificado de fuga
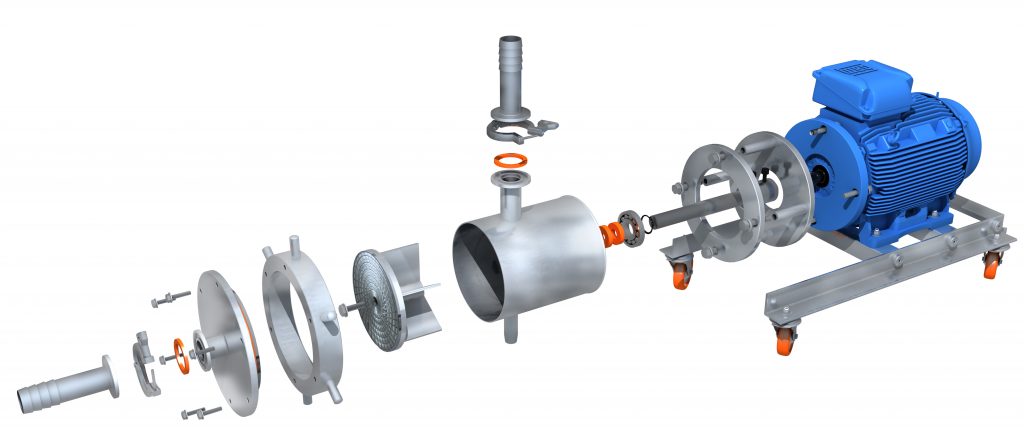
Molinos coloidales
Resuelva su problema de emulsión reduciendo sus costos y aumentando su productividad
Información de contacto
- +54 114754 - 9374
- + 54 11 6351 6288
- info@molinoscoloidales.com.ar
- Calle 28 3332 - San Martín, provincia de Buenos Aires - Rep. Argentina
SOCIAL MEDIA
Todos los derechos reservados. Molinos Coloidales
Diseño web nicolasjpereira