Molinos coloidales
dISPERSORES
dISPERSORES
Una dispersión es una mezcla homogénea de moléculas distintas. En ella aparecen una fase dispersante o disolvente y moléculas dispersas o solutos. En las dispersiones acuosas el agua constituye la fase dispersante, mientras que la fase dispersa presenta amplias variaciones:
Desde pequeñas moléculas como cloruro de sodio, hasta grandes proteínas como las albúminas. Las dispersiones cuya fase dispersa posee moléculas de baja masa molecular se denominan dispersiones coloidales. En el supuesto de que las moléculas de la fase dispersa posean masas moleculares elevadas (más de 10.000 u.m.a.)
O tengan un tamaño comprendido entre 1 y 0,2 micrones, se denominan dispersiones coloidales.
Las dispersiones coloidales pueden presentarse en forma fluida (sol) o con aspecto gelatinoso (gel). El paso de sol
a gel siempre es posible, mientras que el paso inverso no lo es siempre.
- ELECCIÓN DEL DISPERSOR:
- TIPO DE EQUIPAMIENTO
Hay que tener en cuenta el resultado específico que ha de conseguirse con la mezcla. Así, un agitador que sea satisfactorio para estimular la disolución de sólidos solubles en un líquido puede no ser eficaz para mantener sólidos insolubles en una suspensión uniforme.
En muchos casos, el agitador puede necesitarse para realizar dos o más funciones simultáneas:
Buen contacto entre líquidos inmiscibles y al mismo tiempo, ha de estimular la transmisión efectiva de calor al interior del material y desde él.
La selección del mezclador apropiado dependerá también del medio en que se haya de trabajar; ya sea un gas, un líquido o una masa de partículas sólidas; bien sea homogéneo o heterogéneo con respecto a las fases; o las fases; o bien de alta o baja consistencia.
El diseño o proyecto de un agitador exige la especificación del tipo de aparato, las dimensiones y proporciones del elemento mezclador, la situación de este elemento dentro de este recipiente para la mezcla y las condiciones de funcionamiento del agitador. En general, el mezclador óptimo, al igual que el equipo óptimo para otras operaciones unitarias, será el que consiga el resultado deseado con la combinación más económica de cargas fijas y de funcionamiento.
En la práctica se selecciona corrientemente el dispersor que asegura resultados más efectivos y sea más atractivo desde los puntos de vista de su costo instalado y de su conservación, ya que la energía consumida en la mezcla es frecuentemente sólo una pequeña parte de la necesaria para todo el proceso.
No obstante, el proyectista minucioso investigará las necesidades de energía, particularmente en las operaciones que exijan dispersores de gran potencia. El tipo, o los tipos, las dimensiones y la posición del agitador para la
operación se determinan primero partiendo de los principios empíricos generales. Luego se especifican las condiciones de funcionamiento; éstas son menos fáciles de generalizar y se deducen por la experiencia del ingeniero o del vendedor del equipo, o bien por medio de ensayos de modelos.
Aunque existen una gran variedad de mezcladores y dispersores en el mercado, estos pueden ser divididos en aplicaciones de bajo y alto esfuerzo de corte. En la forma, típicamente paletas o tipo propulsores, la reducción del tamaño de la partícula no toma lugar, la acción es realizada por el derretimiento y/o disolución.
El mezclador sirve para mantener la homogeneidad de la composición y la uniformidad de la temperatura, proveyendo un pequeño aumento en si mismo. En el ultimo caso, existe un paso en el cual las partículas son físicamente reducidas en tamaño por el corte mecánico/hidrodinámico con la combinación del rotor/estator acompañado por un pequeño aumento de la temperatura por la energía de mezclado.
Tales equipamientos, aun funcionando con tamaño de partículas superiores a pelletas, proveen rápida y eficiente
dispersión y mezclado.
Equipamiento de alto esfuerzo de corte existen de dos maneras diferentes, tipo inmersión vertical y el del
mezclado en línea.
* El vertical, el rotor/estator esta montado sobre una plataforma e inmerso en un tanque de material, dependiendo
del cabezal mezclador para circular la mezcla y asegurar homogeneidad.
* El caso del mezclado en línea, la combinación del mezclado en un tanque recirculando por una bomba molino.
Experiencias han demostrado que este tipo de equipamiento, lo cual asegura una total disolución, da una mayor rapidez y performance que la desintegración con un solo mezclador vertical, especialmente para grandes volúmenes de producción, tanques mayores a 25 toneladas.
HOMOGENIZADOR-DISPERSOR-DISOLVEDOR HA
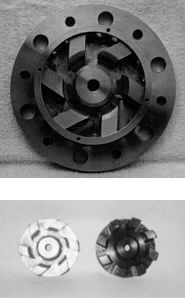
Este modelo se caracteriza por cumplir funciones de: emulsión, dispersión, disolución y homogeneización de productos líquidos, semilíquidos y viscosos. Posee la virtud de romper moléculas y disolver grumos. Se fabrica con motores trifásicos normalizados blindados 100*100 y/o anti – explosivos, cuyas potencias varían de 1 a 7,5 HP (hasta 7.500 rpm) de fabricación Standard., y a pedido se puede llegar a mayores potencias (hasta 150 HP); la velocidad es de 3.000 rpm. La capacidad de mezclado no puede darse en forma definitiva, ya que la mismas depende de distintos factores, como ser:
- Viscosidad
- Densidad
- Producto a mezclar
- Medidas del recipiente
FORMA DE OPERACIÓN:
Se vierte el producto sin refinar en el recipiente, luego se ubica el equipo y se lo coloca en marcha, para agregar a
continuación, el polímero a disolver o por ejemplo, pigmentos, aditivos, vehículos regenerantes, polvos, etc. Está
provisto de una turbina abierta. Posee una cabeza mezcladora que trabaja según el principio de inyección. Los
medios de sujeción pueden ser: bridas, brazos de apoyo, preparado para colgar, etc.
La triple acción positiva explica su superioridad aceptada tanto en su velocidad como eficiencia en agitadores y
disolvedores. Con estos agitadores la acción total esta limitada al mezclado o recirculación del liquido o alguna
solución o mezclados. Las tres etapas del ciclo de mezclado son:
- ETAPA 1:
- ETAPA 2:
- ETAPA 3:
1:Los materiales son colocados por succión en el fondo del cabezal de trabajo Fig.1. y sujetados a una
intensa acción de mezclado por la rotación a alta velocidad de las hojas en el espacio cerrado.
Durante la expulsión desde el cabezal de trabajo, las hojas del rotor sujetan el material a una intensa
acción de corte a la mas alta velocidad, lo que garantiza un extra rápido y total proceso de corte y disolución. La
malla emulsor o el cabezal desintegrador asiste al proceso, disolviendo aglomerados, removiendo grandes
tamaños de partículas de manera que produce emulsiones homogéneas y dispersiones en minutos.
Los materiales procesados son luego expedidos con gran fuerza y velocidad dentro del cuerpo de la
mezcla. Al mismo tiempo el material nuevo ingresa a la base del cabezal mezclador. Esta entrada y salida de las
mezclas indica un patrón de circulación el cual dependerá del tamaño del tanque y el tipo de cabezal o
equipamiento utilizado. El total de la mezcla pasa a través del cabezal mezclador cientos de veces durante el
proceso y la combinación de las tres etapas del ciclo resulta un mezclado positivo, controlado y eficiente. La acción
de la maquina es tan suave que puede ser usada con el liquido a menos de tres centímetros del borde inferior del
tanque. Está completamente libre de vibraciones y de las innecesarias y no deseables características de
turbulencias contra todo otro tipo de mezcladores de alta velocidad. Todas las partes de trabajo están construidas
de acero inoxidable con excepción de los bujes auto lubricados. Son fácilmente limpiables, poco o nulo
mantenimiento siendo necesario.
CABEZAL STANDARD EMULSOR:
Mientras los líquidos están siendo expelidos horizontalmente y el flujo
reflectado sube por el costado de las paredes del tanque, material nuevo está continuamente integrándose dentro
del fondo del cabezal mezclador. La combinación de estos factores determina un patrón de flujo tal como se ilustra
en la figura a la izquierda. Cuando la malla se utiliza en el cabezal emulsor, un intensa acción de corte toma lugar,
dando una eficiente y rápida reducción del tamaño de partículas en suspensiones y tamaño de glóbulo en
emulsiones.
CABEZAL DE FLUJO AXIAL:
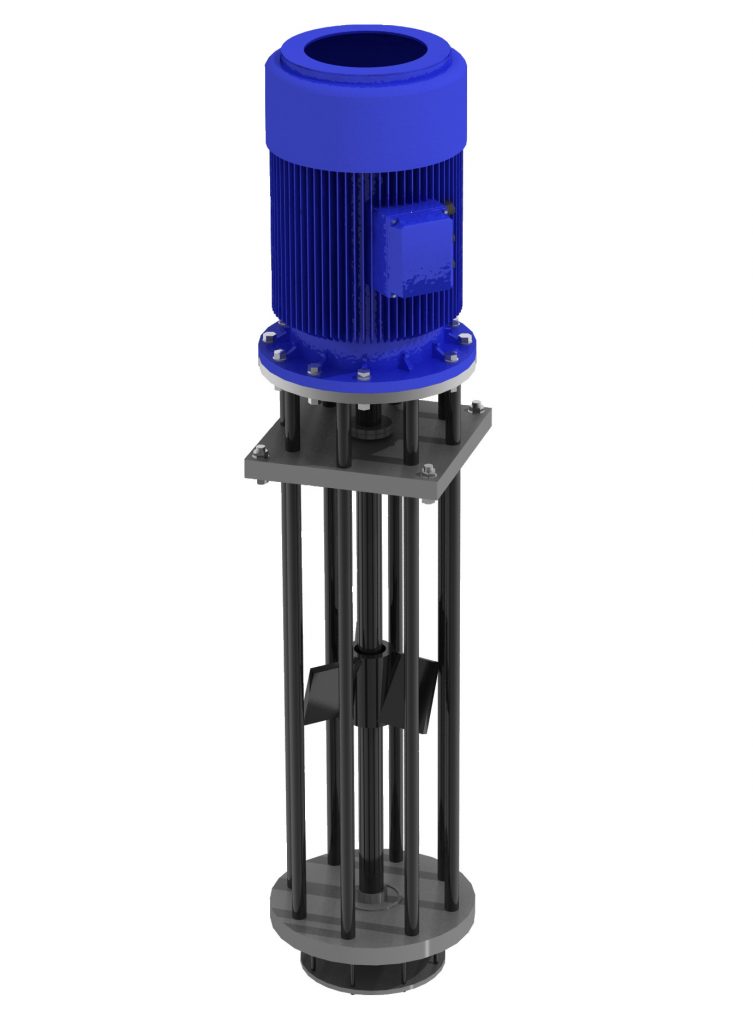
Usado con o sin la malla emulsificante, la mezcla es expelida hacia afuera verticalmente, paralelo al eje del rotor dando el diagrama de flujo. Esta fundamentalmente recomendado para materiales líquidos muy viscoso, previendo la sedimentación de algunos sólidos muy pesados o líquidos inmiscibles durante el procesamiento y aun mas importante para la prevención de la aireación durante el mezclado con altas concentraciones de detergentes. Se utiliza también como deaereador de soluciones muy viscosas.
CABEZAL BOMBEADOR:
Una versión de entrada y salida. El cabezal bombeador puede ser utilizado para
convertir cualquier tipo de rotor a una rápida y accesible bomba que brinda una velocidad de bombeo al menos
igual a las bombas convencionales de la misma potencia. Unos pocos ejemplos son suficientes para demostrar su
valor.
1) Transferencia de la mezcla del tanque mezclador a la máquina de almacenamiento o de llenado.
2) Llenado de pequeños contenedores utilizando uno o más cabezales bombeadores de salida.
3) Recirculación de la mezcla incluyendo el uso del cabezal bombeador como una garantía de que el batch ha sido
procesado.
4) El uso de un segundo rotor para mantener la recirculación y prevenir depósitos mientras la mezcla es bombeada
hacia afuera.
CABEZAL BOMBEADOR
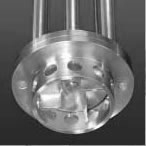
Excelente para procesos de mezclas generales, rápida reducción de partículas sólidas de gran tamaño y flujo vigoroso.
CABEZAL RANURADO
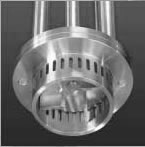
Proporciona la mejor combinación de esfuerzo de corte. Equipado para emulsiones y mezclas de mediana viscosidad
CABEZAL RANURADO RECTANGULARES
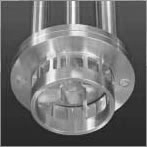
Ideal para aplicaciones que requieren un flujo y esfuerzo de corte importante
MALLA FINA
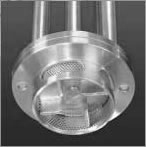
Es ideal para aplicaciones que requieren un flujo y esfuerzo de corte importante
Molinos coloidales
Resuelva su problema de emulsión reduciendo sus costos y aumentando su productividad
Información de contacto
- +54 114754 - 9374
- + 54 11 6351 6288
- info@molinoscoloidales.com.ar
- Calle 28 3332 - San Martín, provincia de Buenos Aires - Rep. Argentina
SOCIAL MEDIA
Todos los derechos reservados. Molinos Coloidales
Diseño web nicolasjpereira